A deep groove ball bearing consists of an inner and outer ring, balls, and a cage that keeps the balls evenly spaced. This design allows the bearing to support both radial and axial loads, making it incredibly versatile and widely used in various applications. The "deep groove" refers to the shape of the raceways that house the balls. These bearings can be open or sealed, with sealed bearings providing protection from dirt, moisture, and contaminants.
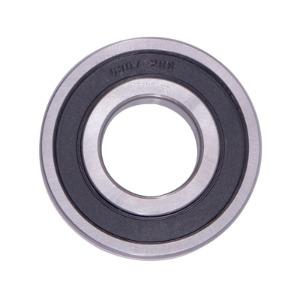
Because of their simple design and effectiveness in handling loads, deep groove ball bearings are found in everything from electric motors and gearboxes to bicycles and automotive components.
The history of ball bearings dates back to ancient times, but deep groove ball bearings as we know them today began to take shape in the late 19th century. The concept of using balls between two surfaces to reduce friction was popularized by Philip Vaughan, who patented the ball bearing design in 1794. However, the deep groove ball bearing, which is more commonly used today, evolved later in the 20th century with the advancement of manufacturing technology.
The initial designs of ball bearings were relatively rudimentary. They were often constructed using steel balls and simple raceways that were manually machined. This early design, while effective, had limitations in terms of performance, precision, and durability. The materials used were not as robust, and the bearings required regular maintenance due to wear and tear.
One of the significant changes in the evolution of deep groove ball bearings has been the improvement in materials used for their construction. Early bearings were made predominantly from steel, which, while strong, was prone to corrosion, wear, and fatigue under heavy loads or conditions.
Alloy Steels: By the mid-20th century, manufacturers began using alloy steels that were alloyed with elements like chromium, manganese, and nickel. These alloys provided enhanced durability, resistance to fatigue, and improved hardness, making the bearings more suitable for high-speed applications.
Ceramic Balls: In the latter half of the 20th century, the introduction of ceramic materials, such as silicon nitride, revolutionized deep groove ball bearings. Ceramic balls are significantly lighter, harder, and more corrosion-resistant than traditional steel balls. They also reduce friction, which allows the bearings to operate at higher speeds while generating less heat. The use of ceramic materials has allowed deep groove ball bearings to perform in more demanding environments, such as in aerospace, medical devices, and high-speed machinery.
Stainless Steel Bearings: Another major advancement has been the development of stainless steel deep groove ball bearings. Stainless steel offers resistance to corrosion, making it an ideal choice for applications exposed to moisture or chemicals. These bearings are widely used in the food processing, marine, and pharmaceutical industries, where hygiene and resistance to corrosive elements are essential.
The design of deep groove ball bearings has also undergone significant refinement to meet the growing demands of modern industries. While the basic structure remains relatively unchanged, the bearings have been optimized in several ways to improve performance and extend lifespan.
Sealing and Shielding: One of the important developments has been the addition of seals and shields to deep groove ball bearings. Early ball bearings were often open, leaving the balls and raceways exposed to contaminants like dirt, water, and debris. This led to wear and failure in harsh environments. Sealed bearings, which incorporate rubber or metal seals around the edges, protect the bearing from contamination and reduce the need for maintenance. This enhancement has made deep groove ball bearings ideal for use in more challenging conditions, including in automotive, industrial, and household applications.
Lubrication: Lubrication is critical to the longevity and efficiency of bearings. Initially, deep groove ball bearings required manual lubrication, which could be inconsistent. Over time, manufacturers developed more efficient lubrication methods, such as grease-filled bearings and oil-sealed bearings. These methods reduce friction, minimize wear, and allow the bearings to run longer without maintenance.