Deep groove ball bearings are one of the common types of bearings used in various industrial applications, including automotive, machinery, robotics, and household appliances. These bearings are renowned for their ability to handle both radial and axial loads while maintaining smooth rotational movement with minimal friction. The performance and longevity of these bearings depend significantly on the quality of their surface finish. One key process that affects the performance of deep groove ball bearings is surface polishing.
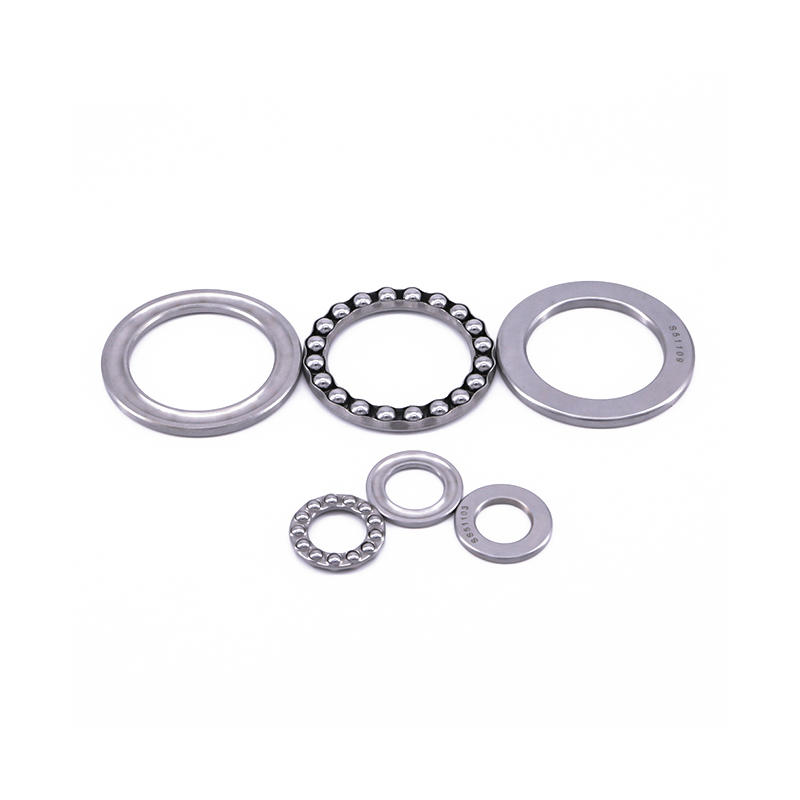
Polishing is distinct from other surface treatments, such as grinding, because it aims for an ultra-smooth finish without altering the geometry of the bearing components. This step is essential for achieving the desired performance characteristics, including reduced wear, lower operating temperatures, and increased service life.
Surface polishing plays a crucial role in the performance of deep groove ball bearings. Below are some of the primary reasons why surface polishing is an important step in bearing production:
1. Reduced Friction and Wear
The main function of a bearing is to reduce friction between moving parts. Any irregularities or roughness on the bearing surfaces can create additional friction, which bring about increased wear and heat generation. By polishing the surface, the bearing components can achieve a smoother interaction, reducing friction and extending the lifespan of the bearing. This is especially important in high-speed applications where low friction is critical for maintaining efficiency.
2. Improved Load Distribution
When the rolling elements of a deep groove ball bearing come into contact with the raceways, the load is distributed across the contact area. A smoother surface ensures that this load is spread evenly, preventing localized stress points that could bring about premature bearing failure. Polished surfaces promote more uniform contact, reducing the risk of pitting, brinelling, or other forms of surface damage.
3. Enhanced Corrosion Resistance
A polished surface is less likely to accumulate contaminants such as dirt, dust, and moisture. This is particularly important in applications where bearings are exposed to harsh environments, such as in the automotive or manufacturing industries. By removing surface imperfections and achieving a smooth finish, polishing can also improve the bearing's resistance to corrosion and environmental damage.
4. Higher Rotational Speed and Efficiency
Deep groove ball bearings are often used in high-speed applications, and the smoothness of the bearing surfaces directly impacts its ability to rotate at high speeds with minimal resistance. Polished surfaces result in lower friction, which allows the bearing to achieve higher rotational speeds while maintaining efficiency. This is critical in industries where performance and energy efficiency are essential.
5. Noise Reduction
A smoother bearing surface bring about less vibration and noise during operation. The roughness of an unpolished bearing can create irregularities in the motion of the rolling elements, resulting in increased noise levels. Polishing the surface helps reduce this noise, contributing to quieter and more stable bearing operation, which is particularly important in industries like automotive manufacturing, where noise reduction is a key factor.
Surface polishing of deep groove ball bearings is typically carried out after other machining processes, such as grinding, are completed. The goal of polishing is to remove any remaining surface imperfections and achieve a mirror-like finish that enhances the bearing's overall performance. Below are the general steps involved in the surface polishing process for deep groove ball bearings:
1. Preparation and Cleaning
Before polishing begins, it is crucial to thoroughly clean the bearing components to remove any dirt, oil, or grease that may be present. Cleaning ensures that no contaminants are introduced into the polishing process, which could affect the final surface finish. Ultrasonic cleaning or chemical cleaning methods are commonly used to prepare the bearings for polishing.
2. Grinding
The surface polishing process often follows the grinding operation. While grinding is used to remove larger amounts of material and achieve rough dimensional accuracy, polishing is a finer process that smooths out the surface to achieve a higher level of finish. The grinding process typically leaves behind a rougher surface that requires further treatment to ensure bearing performance.
3. Polishing with Abrasive Compounds
The next step is the actual polishing, which involves the use of abrasive compounds. These abrasives are applied to the bearing's raceways and rolling elements using specialized polishing machines. The abrasive compounds are usually in the form of pastes, powders, or slurry, and they are selected based on the material of the bearing and the desired finish.