Needle bearings manufacturer are a specialized type of roller bearing characterized by their slender, cylindrical rollers. They are widely used in applications where space is limited but high load capacity and precision are essential. Their unique design allows them to support heavy radial loads while maintaining a compact profile, making them indispensable in automotive transmissions, industrial machinery, and aerospace components. Choosing the right needle bearing is crucial for ensuring system reliability, performance, and longevity.
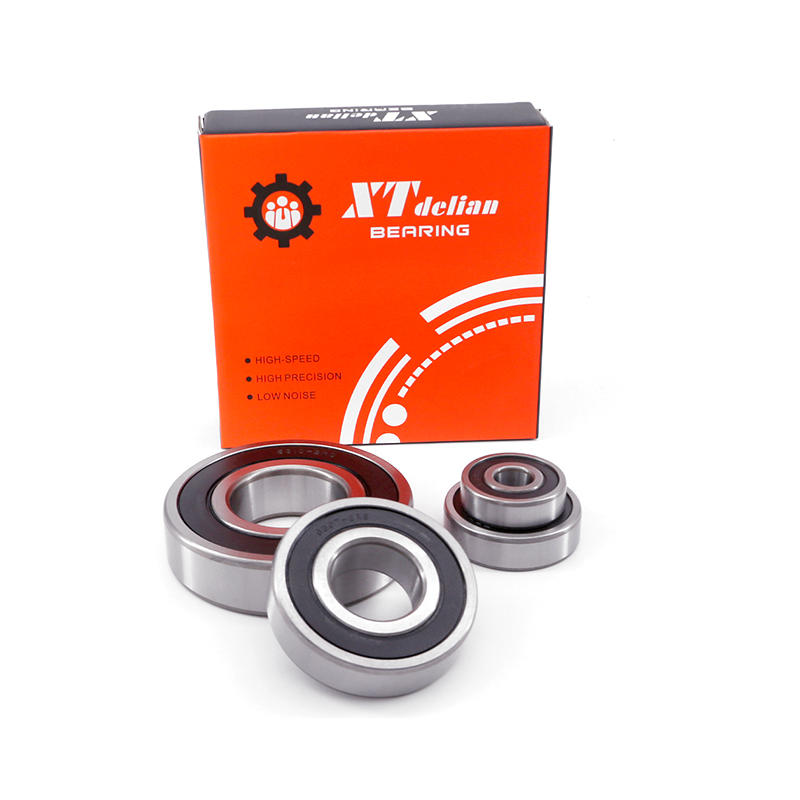
Needle bearings differ from other roller bearings mainly due to the ratio of their roller length to diameter. The rollers are long and thin, resembling needles, which allows for a larger contact surface area relative to the bearing's cross-section. This design translates into high load capacity within a small radial space, ideal for tight assemblies.
There are several types of needle bearings, including:
Full complement needle bearings (without an inner ring)
Needle roller and cage assemblies
Needle roller bearings with inner rings
Drawn cup needle roller bearings
Each type serves different application needs and installation conditions.
Needle bearings are primarily designed to handle radial loads. Understanding the magnitude and nature of the load is essential.
Radial Load: The force acting perpendicular to the shaft. Needle bearings excel at supporting high radial loads due to the increased contact area.
Axial Load: Needle bearings generally have limited axial load capacity unless combined with thrust bearings or specially designed variants.
Accurate load assessment ensures that the bearing selected can handle operating stresses without premature failure.
Dimensions play a vital role, especially because needle bearings are often chosen for their compact size.
Bore Diameter: Must match the shaft size precisely for proper fit and performance.
Outer Diameter and Width: These must fit within the available housing space.
Needle Roller Length and Diameter: Affect load capacity and friction characteristics.
Dimension standards are often guided by manufacturer catalogs or industry standards such as ISO.
Selecting the correct bearing type depends on installation constraints and application specifics.
Full Complement Bearings: Contain the number of rollers,load capacity. They lack an inner ring and require a hardened shaft surface.
Needle Roller and Cage Assemblies: Include a cage that spaces rollers evenly, reducing friction and allowing higher speeds.
Drawn Cup Bearings: Have a thin-walled outer ring formed by deep drawing, making them lightweight and suitable for applications with limited radial space.
With Inner Rings: Provide ease of assembly when shafts are not hardened or cannot be used as raceways.
Needle bearings vary in their speed capabilities depending on design and lubrication.
Bearings with cages generally support higher speeds by reducing friction between rollers.
Full complement bearings handle higher loads but may have lower speed limits.
Lubrication quality and type (oil or grease) also impact speed capability.
Ensure the bearing can operate effectively at the required speed without excessive heat buildup.
Proper lubrication is critical for needle bearing longevity and performance.
Some needle bearings come pre-lubricated with grease for maintenance-free operation.
Others require regular lubrication with appropriate oils or greases based on operating conditions.
Consideration of sealing methods is important to prevent contamination and retain lubricant.
Maintenance intervals and ease of access influence bearing choice, especially in demanding environments.
The operating environment affects material and sealing requirements.
Temperature: High-temperature applications may require special grease and heat-resistant materials.
Contamination: Dusty or wet conditions demand robust seals and corrosion-resistant materials.
Shock Loads: Environments with impact or vibration need bearings with high dynamic load ratings.
Choosing bearings with the right materials and seals enhances reliability.